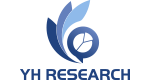
Published Date: 2025-07-04
According to the latest data from YH Research, the global new energy battery industry chain will expand at an accelerated pace in 2025, and the demand for battery-grade nickel sulfate, a key precursor material for cathodes, will show strong growth. Data predicts that in 2025, the total global demand for nickel sulfate will reach 1.1 million tons, an increase of 18% year-on-year, of which battery-grade nickel sulfate will exceed 70% for the first time. Meanwhile, major breakthroughs in high-nickel electroplating sludge resource utilization technology have opened up a new, low-cost, and environmentally friendly raw material pathway for nickel sulfate production. It is estimated that by 2025, nickel sulfate produced via the sludge route will account for 12% of the industry's total production capacity, a significant increase of 8 percentage points compared to 2020, thereby reshaping the industry's competitive landscape.
I. Raw Material Structure Innovation: The Rise of High-Nickel Electroplating Sludge Resource Utilization Pathways
According to relevant report data, high-nickel electroplating sludge contains abundant metal resources, with a nickel content as high as 29.55%, and is accompanied by valuable metals such as copper, iron, and aluminum. Through a complete process chain involving “sulfuric acid leaching — oxidation precipitation to remove iron — sulfidation precipitation to remove copper — nickel hydroxide precipitation — sulfuric acid dissolution — P2O4 extraction for deep impurity removal,” a high recovery rate of 99.84% for nickel can be achieved. According to a full-process metal balance calculation, processing 1 ton of dry sludge can produce 0.29 tons of hexahydrate nickel sulfate. Compared to traditional ore extraction routes, this process reduces energy consumption by 35% and carbon emissions by 42%, aligning with the green development requirements under the current “dual carbon” goals.
II. Impurity Removal Process Upgrades: Breakthrough in Efficient Separation of Iron, Copper, and Aluminum
In the nickel sulfate production process, the impurity removal stage directly determines product purity. Experimental data shows: In the oxidation precipitation iron removal process, when the final pH value is controlled at 3, iron precipitation efficiency reaches 96.03%, with nickel loss rate below 0.5%; In the copper removal stage using sulfide precipitation, when the sodium sulfide excess coefficient is set to 1.2, the copper precipitation rate reaches 99.57%, and the nickel co-precipitation rate is only 6.59%; in the nickel hydroxide precipitation step, when the pH value is 13, the nickel precipitation rate reaches 99.99%, and the aluminum residue rate is 1.09%. Through a three-stage impurity removal system, the total impurity content can be controlled below 0.05%, fully meeting the stringent industry standards for battery-grade nickel sulfate.
III. Deep Purification Innovation: Optimization of P204 Extraction and Separation Technology
Using a P204-260# solvent oil system with a 30% saponification rate, two-stage countercurrent extraction is conducted under pH=4 and O/A=2:1 conditions, achieving efficient impurity separation: copper extraction rate reaches 98.41%, with residual concentration as low as 0.01 g/L; iron extraction rate is 99.99%, residual concentration as low as 0.01 mg/L; aluminum extraction rate of 95.15%, residual concentration of 0.047 g/L, and nickel extraction rate controlled at 9.4%, with the main metal loss rate maintained below 10%. After evaporation concentration and cooling crystallization treatment, the purity of nickel sulfate can reach 99.95%, with total impurities below 500 ppm.
4. Optimization of crystallization process: synergistic control of evaporation concentration and cooling crystallization
The crystallization stage employs a two-stage temperature control strategy: first, evaporation concentration is conducted at 100°C to reduce the solution volume to 1/10 of the original volume, thereby increasing the nickel concentration to 220 g/L; subsequently, the temperature is gradually lowered to 25°C for crystallization, effectively controlling the average crystal particle size between 200–300 μm. XRD phase analysis shows that the product consists of a single hexahydrate nickel sulfate phase with no impurity diffraction peaks. ICP-OES full-element analysis confirms that the residual levels of iron, copper, and aluminum are below 0.0019%, 0.0019%, and 0.0023%, respectively, fully meeting the requirements of the GB/T 26524-2022 battery-grade standard.
5. Green Production Advantages: Comparison of Energy Consumption and Carbon Footprint Across the Entire Process
Compared to the traditional high-pressure acid leaching process for laterite nickel ore, the electroplating sludge resource utilization process demonstrates significant environmental and cost advantages. Comprehensive energy consumption has decreased from 12.5 tons of standard coal per ton of nickel sulfate to 8.1 tons of standard coal; water consumption has decreased from 35 tons per ton to 18 tons; and carbon emissions have decreased from 4.8 tons of CO₂ per ton to 2.7 tons. Life cycle assessment indicates that the carbon footprint of nickel sulfate produced via the sludge route is only 56% of that from the traditional route, fully compliant with the EU Battery Regulation's requirements for sustainable raw materials.
6. Market Application Prospects: Value Release in the New Energy Industry Chain
By 2025, the market price of battery-grade nickel sulfate is expected to stabilize within the range of 28,000–32,000 yuan per ton. According to calculations, the raw material cost of nickel sulfate produced via the sludge route is 0.8 ten thousand yuan per ton (including sludge treatment fees and auxiliary material costs), with processing costs of 1.2 ten thousand yuan per ton (covering energy, labor, and equipment depreciation), resulting in a comprehensive cost of 2.0 ten thousand yuan per ton, offering over a 30% profit margin compared to market prices. It is estimated that by 2025, this route will supply 132,000 tons of battery-grade nickel sulfate, sufficient to meet the production needs of approximately 60 GWh of high-nickel ternary batteries.
By 2025, the nickel sulfate industry will undergo systemic transformations in raw material structure, process technology, and market landscape. High-nickel electroplating sludge resource recovery technology, with its significant advantages of high recovery rates, high purity, and low carbon emissions, has become a key growth driver for the industry. As demand for new energy batteries continues to rise, this green technology route will accelerate the industry's transition toward a low-carbon circular economy. In the future, technological breakthroughs in areas such as extractant regeneration and crystallization mother liquor recycling will further enhance resource utilization efficiency and environmental benefits, warranting close attention from the industry.
The above data can be found in the “2025 Global and China Nickel Sulfate Industry Leading Enterprises Market Share and Ranking Research Report” published by YH Research. YH Research provides in-depth industry research reports, business plans, feasibility studies, customized services, and other one-stop industry consulting services.