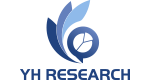
Published Date: 2025-07-02
According to the stand-up forklift market report released by YH Research, this report provides the situation, definition, classification, application, and industrial chain structure of the stand-up forklift market. It also discusses development policies and plans, manufacturing processes, and cost structures, and analyzes the current development status and future market trends of the stand-up forklift market. It analyzes the main production areas, main consumption areas, and main manufacturers of the stand-up forklift market from the perspectives of production and consumption.
Stand-up Forklift Trucks
Against the backdrop of e-commerce order volumes growing at an annual rate of 20% and the continuous expansion of global warehouse space, material handling equipment is undergoing a profound transformation from “labor-dependent” to “smart collaboration.” Stand-up forklift trucks—a type of equipment operated by an operator standing upright, specifically designed for high-frequency, short-distance material handling—have become the “invisible lifeline” of factories, ports, airports, and other scenarios due to their flexibility, efficiency, and safety. The global market size for stand-up forklifts is projected to reach 11.9 billion yuan by 2031, with a compound annual growth rate of 4.7% (2025-2031).
I. Technological Core
1. Power Revolution: The Comprehensive Replacement of Electric Drive
Traditional diesel-powered forklifts, which are noisy and emit high levels of pollutants, are gradually being replaced by electric drive systems. By 2024, electric-powered stand-up forklifts accounted for 78% of the global market, with their core advantages including:
Widespread adoption of lithium-ion batteries: Compared to lead-acid batteries, lithium-ion batteries reduce charging time by 60% (from 8 hours to 3 hours) and extend battery life by three times (from 1,500 cycles to 5,000 cycles), enabling forklifts to achieve “24/7 continuous operation”;
Energy recovery systems: Some high-end models (such as Toyota's Traigo series) recover energy during braking, reducing energy consumption by 15%-20%.
2. Control innovation: From “manual” to “human-machine collaboration”
The control systems of stand-up forklifts are undergoing a three-stage evolution:
Basic mechanical control: Operated via hydraulic levers and a steering wheel, suitable for low-frequency scenarios;
Electronic Power Steering (EPS): Reduces operator physical exertion by 30% and improves precision;
Intelligent Assisted Driving: Integrates cameras, radar, and AI algorithms to achieve automatic obstacle avoidance and path planning (e.g., Jungheinrich's ETV Q series can autonomously plan the optimal transport route).
3. Safety Upgrades: From Passive Protection to Active Warning
Safety is the core selling point of stand-up forklifts. Modern models generally feature:
Operator detection system: Monitors the operator's status via seat sensors and cameras, automatically slowing down when fatigue or absence is detected;
Load stability control: Uses gyroscopes to monitor the tilt angle of the forks in real time, automatically locking when exceeding limits;
Collision warning: Combines ultrasonic sensors and LED warning lights to alert obstacles from 3 meters away.
II. Market Landscape
1. Global Market: Japan and Germany Dominate, with High Technical Barriers
The top five global manufacturers (Toyota, Kion, Jungheinrich, Hitachi, and Crown Equipment) hold a 52% market share, with their core competitive advantages lying in:
Technical Accumulation: Toyota's ACS (Advanced Control System) enables 0.1-meter-level precise positioning;
Global service network: Kion operates 1,200 service centers worldwide with response times of ≤4 hours;
Vertical integration capabilities: Jungheinrich develops its own batteries, motors, and control systems, reducing costs by 20% compared to purchasing from external suppliers.
2. Chinese Market: Domestic Brands Break Through with Cost-Effectiveness
Price advantage: The average price of domestically produced electric forklifts is 40% lower than imported models (150,000–200,000 RMB vs. 250,000–300,000 RMB);
Customization Capabilities: Hangcha Group has developed a “narrow aisle-specific model” for e-commerce warehouses, requiring only a 2.2-meter aisle width;
Policy Benefits: China's 14th Five-Year Plan for Intelligent Manufacturing explicitly supports forklift electrification, with electric forklift subsidies reaching 15% of the sales price by 2024.
III. Future Trends
1. Automation: From “manned operation” to “unmanned operation”
Automatic forklifts (AGV/AMR) are becoming the upgrade direction for stand-up forklifts. The global market size for automatic stand-up forklifts is expected to reach 230 million yuan in 2024 and exceed 500 million yuan by 2031. Typical examples include:
Clark Material Handling's C-AGV series: Achieves autonomous material handling via laser navigation with positioning accuracy of ±5mm;
Hyundai Heavy Industries' Hi-MATE system: Supports multi-vehicle collaborative scheduling, increasing warehouse utilization by 30%.
2. Intelligence: Integration of IoT and Predictive Maintenance
Forklifts are transitioning from “independent devices” to “smart terminals”:
Telematics systems: Real-time upload of operational data (such as operating time, fault codes) to the cloud; Toyota's “i-Forklift” platform can predict motor failures 72 hours in advance;
Digital twin technology: Simulates forklift operations via virtual models to optimize maintenance schedules, reducing downtime by 40%.
3. Greenification: Exploring Hydrogen Fuel Cells and Battery Swapping Models
To overcome the range limitations of lithium-ion batteries, the industry is piloting:
Hydrogen Fuel Cells: Komatsu Group's FCXT series forklifts can be refueled in just 3 minutes and have an 8-hour range;
Battery Swapping Models: China Longgong has launched a “vehicle-battery separation” service, allowing users to lease batteries and reduce initial costs by 30%.
IV. Challenges and Recommendations
1. Core Challenges
Technology Gap: High-end sensors (such as lidar) still rely on imports, with domestic substitution rates below 30%;
Standard Deficiencies: Safety standards for automated forklifts (such as ISO 3691-4) have not yet been mandatorily implemented in China;
Customer Perception: Small and medium-sized enterprises have concerns about the return on investment cycle for intelligent forklifts (typically 3-5 years).
2. Practical Recommendations
Corporate Level:
Focus on developing specialized models for niche scenarios (e.g., cold chain, hazardous chemical warehouses);
Collaborate with logistics system integrators (e.g., Dematic, Daifuku) to provide an integrated “forklift + WMS” solution.
Investor Level:
Focus on companies with end-to-end capabilities in both hardware and software (e.g., Jungheinrich);
Invest in emerging technology sectors such as hydrogen fuel cells and battery swapping.
Policy-maker level:
Introduce subsidies for automated forklifts (e.g., tax breaks equivalent to 20% of investment amounts);
Promote the establishment of an internationally recognized safety certification system.
Conclusion
From manual handling to intelligent collaboration, the evolution of stand-up forklifts reflects the global manufacturing industry's relentless pursuit of efficiency and safety. Facing a market opportunity of 11.9 billion yuan by 2031, companies must break through cost barriers through technological innovation and build service barriers through ecosystem collaboration. Policy makers, meanwhile, must accelerate the transition of this “logistics cornerstone” toward its ultimate green and intelligent form through standard-setting guidance and subsidy support. In this transformation, those who can first balance efficiency, cost, and sustainability will dominate the material handling market in the next decade.