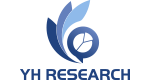
Published Date: 2025-06-30
According to the hot wedge welding machine market report released by YH Research, this report provides the situation, definition, classification, application, and industrial chain structure of the hot wedge welding machine market. It also discusses development policies and plans, manufacturing processes, and cost structures, and analyzes the current development status and future market trends of the hot wedge welding machine market. It also analyzes the main production regions, main consumption regions, and major manufacturers of the hot wedge welding machine market from both production and consumption perspectives.
I. Market Size and Growth Drivers: Infrastructure Investment Drives a Hundred-Billion-Yuan Market Segment
According to the latest data from YH Research, the global hot wedge welding machine market size reached 8.7 billion yuan in 2024 and is expected to expand to 14.13 billion yuan by 2031 at a compound annual growth rate (CAGR) of 7.0%. Behind this growth is the combined effect of increased global infrastructure investment, upgraded environmental protection engineering standards, and the expansion of thermoplastic material application scenarios. As core equipment for geotechnical waterproofing and municipal waterproofing projects, hot wedge welders achieve material fusion welding through wedge-shaped heating elements, with weld seam strength exceeding 80% of the base material. They have become standard tools for “new infrastructure” projects such as water conservancy and hydropower, and transportation tunnels.
II. Policy Variables: Supply Chain Restructuring Amid Tariff Negotiations
The 2025 U.S. tariff policy adjustments are triggering a chain reaction in the welding equipment supply chain. On one hand, increased import tariffs have caused equipment costs in the North American market to rise by 10%-15%, putting procurement pressure on small and medium-sized construction companies. On the other hand, European manufacturers like Leister Technologies are accelerating the establishment of production bases in Mexico to leverage the U.S.-Mexico-Canada Agreement (USMCA) to avoid tariff barriers. Meanwhile, Chinese manufacturers like Hebei Mingmai Technology are breaking into the Southeast Asian market through a “Southeast Asian manufacturing + localized service” model, with export revenue growing by 22% year-on-year in 2024.
III. Technological Evolution: The Transition from Mechanical Welding to Smart IoT
The current market presents three major technological trends:
Automation Upgrades: Miller Weldmaster's AW-6000 series integrates laser positioning and pressure feedback systems, controlling weld seam straightness deviation within ±0.5mm;
Energy Revolution: NAUE GmbH has developed solar-assisted heating modules, reducing equipment energy consumption by 40% and adapting to off-grid construction sites in Africa;
IoT integration: Weldy's SmartWeld platform uses 4G modules to enable remote parameter monitoring, increasing equipment utilization by 35%.
Technological integration has become a new competitive arena. Emabond Solutions' AI weld detection system can real-time identify virtual weld defects with a false positive rate below 0.3%, and is expected to capture 25% of the high-end market by 2026.
IV. Competitive Landscape: European and American Manufacturers Lead, Chinese Firms Break Through
The top 20 global manufacturers account for over 75% of the market share, forming a “three-tier” competitive landscape:
First tier: Leister Technologies (22%) and Miller Weldmaster (18%) dominate the high-end market through their full-industry-chain布局;
Second tier: BAK Technology (12%) and Foremost Machine (10%) have established technical barriers in the geomembrane welding field;
Chinese Players: Hebei Mingmai (8%) and Fuzhou Leister (7%) are capturing emerging markets through cost-effectiveness advantages and gradually entering the supply chain for European water conservancy projects.
Chinese manufacturers are breaking through technological barriers. Hebei Mingmai's independently developed carbon fiber heating components have doubled the equipment's heating speed, securing an order for 300 units from China Construction Group.
5. Regional Markets: Diversifying Demand and Cultivating Growth Poles
North America: As the largest consumer market (accounting for 35%), growth may slow to 6.5% by 2025 due to tariff policies, but the Infrastructure Bill is driving the update of municipal waterproofing equipment;
Europe: Germany's Circular Economy Act requires a 70% recycling rate for construction waste, driving annual demand for waterproof membrane welding equipment exceeding 20,000 units;
China: Policy benefits are being released, with the 14th Five-Year Plan for flood control projects driving annual equipment demand growth of 18%;
Emerging Markets: India's water conservancy investment is growing at an annual rate of 12%, driving a CAGR of 9% for hot wedge welding machine demand, making it a key focus area for Foremost Machine.
6. Application Scenario Expansion: From Waterproofing Projects to Ecological Restoration
Beyond traditional infrastructure sectors, equipment is penetrating into:
New Energy Infrastructure: GCL Group used NAUE welders to complete HDPE membrane welding at its Kubuqi Desert photovoltaic base, extending component lifespan by five years;
Mine restoration: Zijin Mining used Weldin Equipments devices for tailings pond waterproofing, improving heavy metal pollution interception efficiency by 60%;
Emergency rescue: China Aneng Group equipped portable hot wedge welders, reducing post-disaster waterproofing barrier construction time by 70%.
7. In-Depth Case Study: Leister Technology Empowering the Sichuan-Tibet Railway Waterproofing Project
In 2024, Leister Technologies provided customized welding machine solutions for the Ya'an section of the Sichuan-Tibet Railway, achieving breakthroughs through the following innovations:
High-altitude adaptability: Adopting a turbocharged cooling system enables the equipment to operate stably at an altitude of 5,000 meters;
Intelligent temperature control: Integrating an infrared temperature measurement module reduces the standard deviation of EVA waterproof sheet welding penetration depth to 0.2 mm;
Construction Management: Utilizing an IoT platform to coordinate the scheduling of 50 devices, achieving a daily welding mileage exceeding 800 meters.
This case study reduced the project timeline by 20% and was awarded the “Annual Technical Breakthrough Award” by Engineering Machinery Weekly.
8. Future Challenges and Opportunities: Localized Innovation and Green Transformation
Current industry pain points include:
Operational barriers: Only 30% of construction personnel can achieve optimal welding parameters. Miller Weldmaster introduced an AR training system, increasing the qualification rate to 85%;
Material compatibility: Welding of new TPU waterproof membranes is prone to burning. Hebei Mingmai developed a pulse heating module, increasing the yield rate to 98%;
Emerging technology disruption: Laser welding technology is diverting the high-end market, requiring hot wedge welders to specialize in specific application scenarios.
2025-2031 Development Trend Forecast:
Service-oriented transformation: Equipment sales are shifting toward a “hardware + construction services” model, with service revenue expected to exceed 40% by 2028;
AI-enabled: Features such as automatic weld quality rating and adaptive temperature control are becoming standard, with Leister having applied for 39 related patents;
Lower-tier markets: 5G + remote control technology lowers the barrier to equipment operation, opening up emerging markets such as Africa and Latin America.
IX. Industry Insights: Balancing Innovation and Compliance
Facing the triple transformation of tariff policies, technological iteration, and market demand, companies need to build three core capabilities:
Supply chain resilience: Diversify risks through regionalized布局, such as Leister establishing a North American supply center in Mexico;
Data assetization: Convert construction data into process optimization solutions, such as BAK Technology's collaboration with China Communications Construction Group to develop a welding parameter database;
Compliance foresight: Proactively align with regulatory requirements such as the EU's Machinery Directive 2023/1230 and China's Special Equipment Safety Law.
Conclusion
The hot wedge welding machine market is at a critical juncture of technological transformation and policy restructuring. Over the next six years, the industry will witness a transition from “construction tools” to “infrastructure intelligent terminals.” The ability to build a digital service ecosystem based on efficient welding will become the core factor determining a manufacturer's market position. For investors, focusing on companies with precision manufacturing capabilities, global compliance experience, and potential for service-oriented transformation may capture the next wave of opportunities in the infrastructure equipment sector.