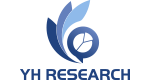
Published Date: 2025-06-19
According to the pad printing silicone market report released by YH Research, this report provides the situation, definition, classification, application, and industrial chain structure of the pad printing silicone market. It also discusses development policies and plans, manufacturing processes, and cost structures, and analyzes the current development status and future market trends of the pad printing silicone market. It also analyzes the main production areas, main consumption areas, and main manufacturers of the pad printing silicone market from the perspectives of production and consumption.
According to YH Research data, the global pad printing silicone market size will reach 1.64 billion yuan in 2024 and is expected to approach 2.5 billion yuan in 2031, with a compound annual growth rate (CAGR) of 6.1% from 2025 to 2031. This growth is primarily driven by three core factors:
Upgrades in the consumer electronics industry: Global shipments of smartphones and wearable devices continue to rise, with the consumer electronics sector accounting for 38% of screen printing silicone demand in 2024 (IDC data). For example, Apple's iPhone 16 series casing printing uses screen printing silicone with a Shore hardness of 40A, with a consumption rate of 0.5 tons per million units.
Refined demands in the packaging industry: The premium cosmetics and food packaging sectors have raised their requirements for printing precision, driving the evolution of screen printing silicone toward higher abrasion resistance and lower shrinkage rates. According to Euromonitor statistics, the global premium packaging market saw a 12% year-on-year increase in screen printing silicone usage in 2024.
Trends in medical device compliance: The FDA's stricter requirements for the clarity of medical device labeling have prompted companies to adopt soft screen printing silicone with a Shore hardness of 10A-25A to accommodate printing on curved medical device surfaces. For example, in the printing of Medtronic pacemaker labels, the usage rate of silicone in this hardness range increased from 15% in 2020 to 32% in 2024.
Impact of U.S. Tariff Policies in 2025 on the Global Supply Chain
Adjustments to U.S. tariff policies in 2025 will have a profound impact on the silicone rubber industry, specifically manifested as follows:
Strengthened regional trade barriers: The U.S. imposes tariffs of 15%-25% on imported specialty rubber materials, leading to a 18%-23% increase in costs in the North American market. For example, CHT Germany GmbH was forced to raise the price of its screen printing silicone exported to the U.S. by 20%, resulting in a decline in market share from 27% in 2024 to 24%.
Regional restructuring of supply chains: European manufacturers are accelerating their expansion into Southeast Asia's “zero-tariff zone,” while Chinese manufacturers are entering the Latin American market through a “technology licensing + localized production” model. For example, Shenzhen Jiajinghong Technology has established a screen printing silicone production base in Vietnam, with an expected annual production capacity of 3,000 tons by 2026, covering the Southeast Asian and Australian markets.
Breakthroughs in domestic substitution technology: To circumvent tariff barriers, domestic manufacturers are intensifying R&D efforts on high-hardness, low-volatility screen printing silicone. For example, Guangdong Yongzhuo Technology's product with a Shore hardness of 60A achieves a 25% improvement in wear resistance compared to imported products, with domestic market share rising to 19% by 2024.
Technological evolution and product innovation directions
As a core branch of specialty rubber materials, technical breakthroughs in screen printing silicone rubber are concentrated in three key areas:
Precision hardness grading: By regulating molecular chain structures, precise hardness grading is achieved within the Shore hardness range of 10A to 70A, with each grade differing by 5A. For example, Wacker Chemie AG's dynamic hardness adjustment technology enables hardness fluctuations within the same batch to be controlled within ±1A.
Environmental performance upgrades: Developing low volatile organic compound (VOC) formulations compliant with RoHS and REACH standards. For example, Shenzhen Zheng'an Organic Silicon Materials reduced VOC emissions from 800 ppm in 2020 to 200 ppm by 2024, earning certifications from multiple international brands.
Functional composite development: Integrating properties such as conductivity, antibacterial, and high-temperature resistance to expand application scenarios. For example, Engineered Printing Solutions' conductive screen printing silicone maintains a resistivity of below 10⁻³ Ω·cm in electronic component printing.
Global Market Competition Landscape and Regional Market Characteristics
The global screen printing silicone market presents a competitive landscape characterized by “European and American dominance and Asian-Pacific catch-up.” According to 2024 market share data:
First Tier: Multinational companies such as CHT Germany GmbH and Deco Technology Group dominate the market, accounting for approximately 52% of the total market share. Among them, CHT Germany GmbH holds over 45% of the high-end market share through its comprehensive product portfolio across all hardness ranges.
Second Tier: Asia-Pacific manufacturers such as Shenzhen Jiajinghong Technology and Guangdong Yongzhuo Technology collectively hold approximately 28% of the market share, primarily capturing the mid-to-low-end market through cost-effectiveness advantages and customized services.
Emerging Vendors: Companies such as OTT New Materials and Dongguan Taisen Industry collectively hold approximately 20% of the market share, focusing on technological breakthroughs in niche areas.
Regional Market Characteristics:
North America: A technology-driven market with stringent requirements for the abrasion resistance and solvent resistance of screen printing silicone, with high-end products accounting for 68% of the market in 2024.
Europe: An environmentally driven market, the EU's Registration, Evaluation, Authorization, and Restriction of Chemicals (REACH) regulation has promoted the widespread adoption of low-VOC products, with compliant products accounting for over 75% of the market in 2024.
Asia-Pacific: A cost-driven market with strong demand for mid-to-low-end products, but high-end products still rely on imports. For example, the localization rate of products with a Shore hardness of 50A or above in China is less than 40%.
Segment competition and user behavior insights
Hardness range competition differences: Products with Shore hardness of 10A-25A, due to their high softness, account for over 60% of the market share in the medical device and ceramic glass sectors; products with Shore hardness of 50A-70A, due to their high abrasion resistance, account for 55% of the market share in the consumer electronics and packaging industries. For example, Inkcups' Shore hardness 65A products hold a 40% market share in smartphone frame printing, but their price is 35% higher than that of Shore hardness 30A products.
User decision preferences: Large OEM manufacturers prioritize product stability and supply chain responsiveness, while small and medium-sized processing plants prioritize price-sensitive products. For example, a procurement manager from a leading electronics manufacturer stated that when selecting a screen printing silicone supplier, they require the supplier to provide quality stability reports for at least three consecutive production batches.
Future Trends and Industry Challenges
Over the next seven years, the screen printing silicone market will exhibit the following trends:
3D Printing Integration Applications: Developing screen printing silicone materials compatible with 3D printing equipment to achieve one-time printing on complex curved surfaces. For example, Boston Industrial Solutions is currently researching and developing 3D printing-specific silicone, with commercialization expected by 2027.
Bio-based Material Substitution: Using renewable resources to produce screen printing silicone to reduce carbon footprints. For example, Cedrus Silicone's product with 30% bio-based content is currently in the testing phase.
Emerging Market Boom: Rapidly growing demand in regions such as Southeast Asia and the Middle East is becoming a new focal point for manufacturers.
However, the industry still faces three major challenges:
High Technical Barriers: Formulations and processes for high-end hardness range products are still monopolized by European and American companies, with domestic products lagging behind by 20%-30% in performance.
Long certification cycles: The process from R&D to obtaining international certification takes 3-5 years, and small and medium-sized enterprises struggle to bear the high testing costs.
Fluctuating raw material prices: The prices of silicone monomers are influenced by international crude oil prices, with fluctuations reaching 15%-20%, compressing corporate profit margins.
Conclusion
As a core branch of specialty rubber materials, the market growth and technological iteration of screen printing silicone are deeply intertwined with the global manufacturing industry's upgrading needs. Under the dual drivers of tariff policy fluctuations and technological innovation, manufacturers must strengthen regional, deepen industry-academia-research collaboration, and expand into emerging markets to build sustainable competitive advantages. In the future, with the development of precise hardness grading, environmental performance upgrades, and functional integration, the screen printing silicone rubber market is expected to enter a high-quality development phase, providing the global manufacturing industry with more efficient and environmentally friendly surface printing solutions.